In today’s world, technology has woven itself into the fabric of every industry, including manufacturing. The journey towards complete digitization is not a distant future - it's happening now, reshaping businesses both big and small. As enterprises embark on this transformative path, the focus shifts from merely investing in technology to optimizing and profiting from it.
The global manufacturing sector has witnessed a radical shift in recent years. The catalyst for this change was the challenges brought on by the pandemic, which forced the very backbone of global commerce to confront unprecedented disruptions in supply chains. Amidst these trials, technology emerged as more than a tool; it became a lifeline, offering resilience and adaptability in the face of adversity.
The dawn of a new age in digital manufacturing is upon us. Increasingly, manufacturers are embracing this shift, leveraging data-driven insights to propel themselves towards more sustainable and efficient manufacturing practices. For instance, a study by Workday reveals that automation can reduce planning and reporting cycles in manufacturing by a staggering 50%-70%.
“The future of manufacturing is digital. Those who embrace technology will succeed, while those who resist will be left behind.”
– Klaus Schwab, Founder of the World Economic Forum
To capitalize on the opportunities and embrace smart manufacturing, manufacturers need a well-defined IT strategy that enables them to be more resilient than ever. As far as the digital manufacturing industry is concerned, the year 2023 has been transformative, with widespread and accelerated adoption of technologies like AI, data analytics, cloud computing, edge computing, and more that allow automation “at the source,” thereby enhancing efficiency with less dependency on centralized servers.
Top digital manufacturing trends to expect in 2024
The manufacturing industry stands on the brink of a transformative era defined by three pivotal pillars:
1. Connectivity: The backbone of modern manufacturing, connectivity ensures seamless integration and communication across various systems and processes.
2. Intelligent automation: This is the driving force behind smarter operations, leveraging AI and robotics to enhance efficiency and precision.
3. Scalable data management & analytics: The ability to manage vast amounts of data and extract actionable insights is critical for strategic decision-making and continuous improvement.
Within these domains lies a spectrum of technologies poised to redefine manufacturing. These range from IoT devices that offer real-time monitoring to advanced analytics that predict maintenance needs, and from AI-driven automation that optimizes production to scalable cloud infrastructures that support the ever-growing data demands.
For manufacturers to thrive amidst rapid industrial evolution, it’s crucial to not only watch these trends but to actively incorporate them. We invite you to join the conversation and discover the technologies set to shape the future of manufacturing excellence.
Trend #1: Smart factories will transform shop floors
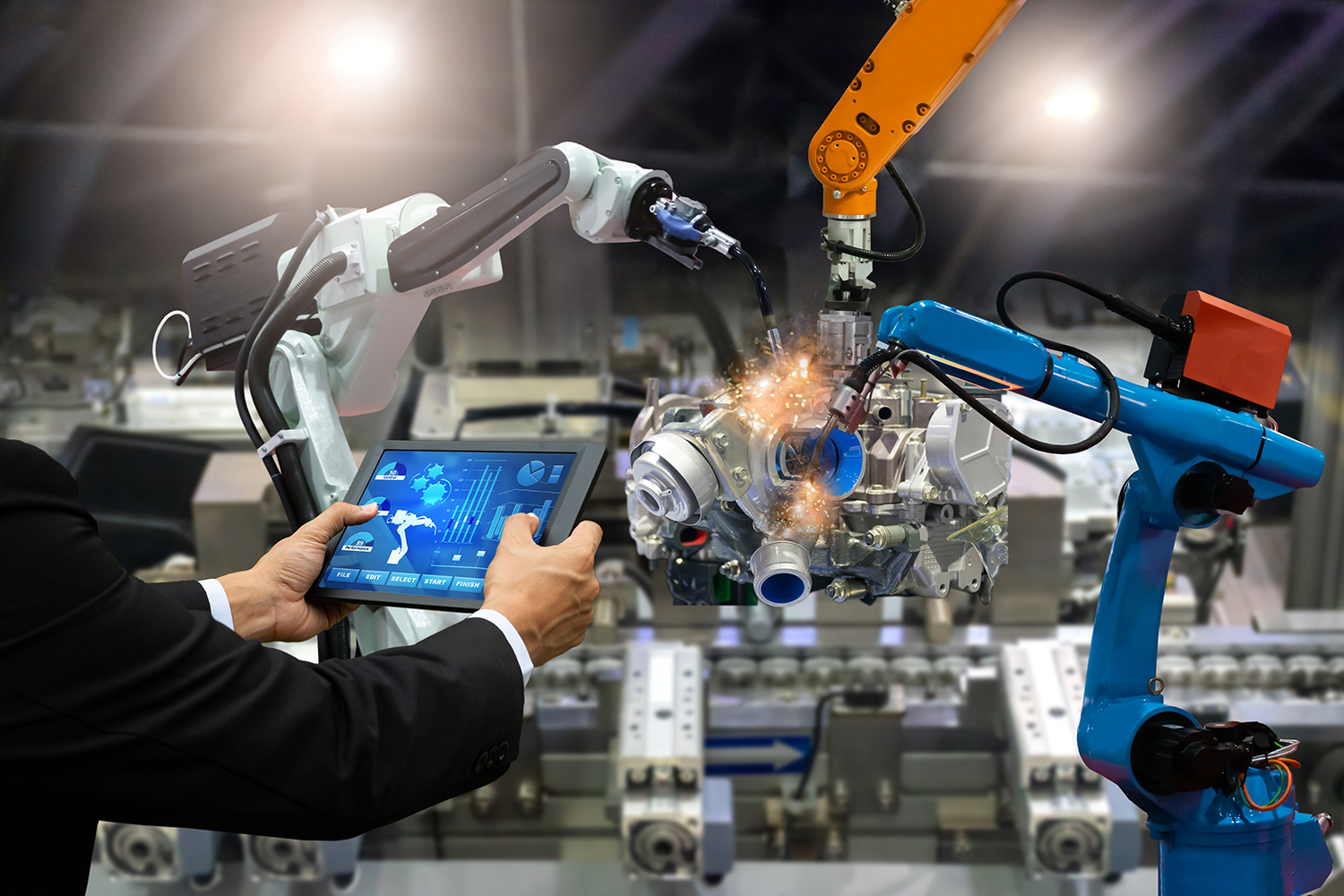
A "smart" factory stands as a highly advanced and automated facility, revolutionizing conventional operations through key technologies like the Industrial Internet of Things (IIoT), Artificial Intelligence (AI), automation, and digital twins. Projections indicate that the global smart factory market is poised to reach approximately $321.98 billion by 2032, with a CAGR of 9.52% from 2023 to 2032.
Smart factories enhance efficiency and production processes by utilizing interconnected devices, real-time analytics, and smart sensors. Today, smart factories have found applications across diverse industries, including energy, power, automotive, oil and gas, electronics, and semiconductors. For instance, the Tesla Gigafactory in Germany integrates solar panels to promote sustainability and reduce operating costs. Similarly, BJC Healthcare in the US has adopted smart manufacturing that incorporates IoT into its processes. The company employs Radio Frequency Identification (RFID) technology to track medical supplies. The implementation of a smart factory has enabled them to reduce costs, increase operational efficiency, and overall improve the company’s functionality.
Rise of digital twin technology
The evolution of cutting-edge technologies also fuels the rise of digital twin technology in manufacturing, creating a digital replica of physical processes for informed decision-making. Ford's implementation of AI-driven predictive maintenance through digital twin technology serves as a notable example. Ford develops distinct digital twins for each vehicle model, covering various production stages from concept to operation. These digital models extend to manufacturing procedures, production facilities, and the customer experience. Ford's digital twin accurately identifies energy losses, highlights areas for energy conservation, and boosts overall production line performance. The growing popularity of digital twins is reflected in projections, which anticipate a market size of $73.5 billion by 2027.
AI/ML play a crucial role
The strategic use of AI empowers manufacturers to analyze extensive datasets systematically, identify patterns, and facilitate intelligent decision-making. In the supply chain domain, AI plays a crucial role in predictive analytics, optimizing inventory management, refining demand forecasting, and streamlining logistics. This is evident in companies like Amazon, which employs AI-powered algorithms to expedite deliveries, reducing the gap between their products and customers.
AI is influential not only in the supply chain but also in various other areas. This can be seen from the example of the Haier Group, a leading consumer electronics and home appliances manufacturer in China. The group has integrated AI into its manufacturing processes within a smart factory framework. This integration enhances various aspects such as quality detection, maintenance, machine collaboration, material transportation, energy management, and security. This example underscores the multifaceted applications of AI in modern manufacturing, showcasing its potential for operational enhancement and efficiency across diverse industries. The trajectory of AI indicates that Generative AI will play a central role in the years to come.
Notably, discussions about AI are incomplete without addressing machine learning, a crucial component in predictive analytics for quality control. Machine learning algorithms play a substantial role in proactive measures to enhance product quality and optimize manufacturing processes. A significant two-thirds of manufacturing companies attribute substantial revenue savings or generation to machine learning and advanced analytics.
A notable paradigm shift
Additionally, technologies such as Augmented Reality (AR) and Virtual Reality (VR) provide an immersive experience in manufacturing, allowing users to enhance their senses with real-time data from any location, ensuring constant and accurate awareness of the factory's status anywhere, anytime. Furthermore, Web 3.0 enhances machine interactivity through advanced technologies such as AI, deep learning, machine learning, Big Data, and data analysis, enabling machines to comprehend information like humans using language comprehension technologies and the Semantic Web.
In the domain of manufacturing, a notable paradigm shift is underway with the introduction of Collaborative Robots (Cobots). These human-powered robots work alongside humans, contributing to efficiency by providing strength, power, precision, and data. Importantly, AI technology facilitates their ease of programming and quick learning, marking a significant advancement in the manufacturing landscape.
Trend #2: Blockchain technology will subside supply chain challenges
Blockchain technology is truly a transformative tool when it comes to enhancing transparency and security within the digital manufacturing supply chain. Through the creation of a tamper-proof record of transactions, leveraging blockchain in the supply chain enables manufacturers to meticulously trace products throughout their entire lifecycle, from raw materials to finished goods. This robust and unalterable ledger system ensures data integrity and authenticity.
Blockchain also offers manufacturers the opportunity to streamline operations, gain heightened visibility into supply chains, and track assets with unparalleled precision, as revealed by PwC. This is one of the reasons why Walmart, the retail giant that sells everything from furniture to the latest mobile phones, leverages blockchain technology to oversee their suppliers of leafy greens, aiming to guarantee product safety and expedite the process of providing evidence in case of a claim. The system collects data at each stage of the greens' journey, starting with the planting of seeds. Even after the greens reach the shelves, the company can continually contribute data to the platform.
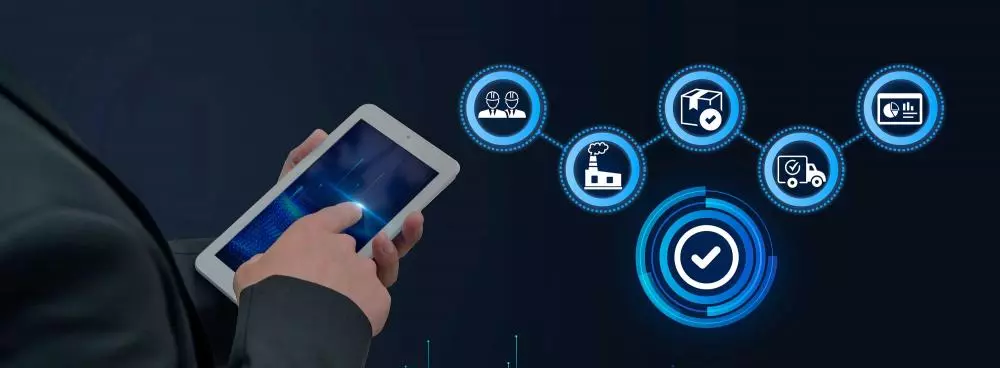
Currently, 24% of industrial manufacturing CEOs are either exploring or implementing this transformative technology. As cybersecurity and data privacy become more critical as a direct result of digital transformation, Blockchain applications are expected to become more prevalent in the manufacturing industry soon.
Other futuristic technologies that will have a major influence on the future of manufacturing over the span of the next 2–10 years include Intelligent Process Automation, Autonomous Mobile Robots, Cobots, AR/VR/MR/metaverse, Web 3.0 and Knowledge Engineering, Intelligent Edge, Neuromorphic computing, 4D Printing, Quantum Computing, 6G and c-band, Zero Trust security, self-diagnosis systems, resilient and self-healing systems, AND Fully Homomorphic Encryption.
Overcoming digital manufacturing challenges can be daunting
Embracing digital transformation has its own challenges for manufacturers. For instance, modernizing legacy systems demands significant investments, including hardware upgrades and standardization of data formats. Efficiently managing diverse data sources requires robust strategies and advanced analytics. Cybersecurity is an important concern as well, necessitating multi-layered defenses and compliance with privacy regulations. Lastly, addressing the skills gap and overcoming resistance to change in the workforce requires targeted training programs, clear communication, and stakeholder engagement for successful digital adoption.
To effectively tackle these challenges, it is imperative for manufacturers to partner with experts who have the combined knowledge and experience of the domain and technology. At InfoVision, we specialize in supporting the expansion of manufacturing to accelerate digital transformation. Over the years, we have helped numerous manufacturers address key challenges with digital transformation, offering solutions in product design, engineering, and cutting-edge technologies like AI, IoT, and mobile app development. Our expertise extends to crucial areas like Blockchain-based supply chains, Data Analytics, smart manufacturing, and more.
The opportunities are endless
As we gaze into the horizons of 2024, the manufacturing industry is poised for a remarkable transformation where a fusion of cutting-edge technologies meets the dynamic challenges of business. This blend is set to revolutionize efficiency and spur innovation like never before. We also expect that the supply chain complexities will be more than just a hurdle; they will act as critical drivers for change, shaping the future of manufacturing in profound ways.
For manufacturers, understanding these shifts is crucial. These are not mere tweaks to existing processes; they represent a paradigm shift, heralding a new epoch in manufacturing execution and strategy. This is more than adaptation; it's a complete reimagining of the manufacturing ethos for 2024 and beyond.
Partner with InfoVision to stay ahead of the curve of transformative shifts in the digital manufacturing industry. Contact us today to learn more.